Avainero PFMEA:n ja DFMEA:n välillä on, että PFMEA auttaa analysoimaan liiketoimintayksikön tietyn prosessin mahdollisia vikoja, kun taas DFMEA auttaa analysoimaan tuotteen suunnittelun mahdollisia vikoja.
FMEA (Failure Mode Effects Analysis) -menetelmä auttaa tunnistamaan prosessin mahdolliset vikatilat toiminnanhallinnassa ja suunnittelussa järjestelmän tuotekehitysvaiheessa ja luokittelemaan viat vian todennäköisyyden ja vakavuuden perusteella. Vikatila tarkoittaa mitä tahansa vikoja tai virheitä suunnittelussa, prosessissa tai tuotteessa, joka vaikuttaa asiakkaaseen. "Vaikutusanalyysi" viittaa epäonnistumisten seurausten tutkimiseen.
Mikä on PFMEA?
PFMEA on lyhenne sanoista Process Failure Mode Effects Analysis. Tällä menetelmällä voidaan tunnistaa mahdolliset vikatilat prosessien toimintatasolla. Yleensä PFMEA:n suorittaa teknisesti kokenut tiimi. Perusprosessi on riittävän tiedon kerääminen vikatilojen syistä vikatilan vaikutusten korjaamiseksi tai minimoimiseksi.
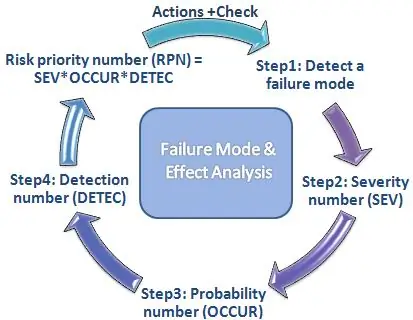
Lisäksi PFMEA on jäsennelty työkalu, jota käyttävät kaikenlaiset organisaatiot. Se auttaa rakentamaan vikatilojen vaikutuksia ja priorisoi riskin lieventämiseen tarvittavat toimenpiteet. PFMEA dokumentoidaan ja esitetään ennen uusien prosessien käynnistämistä mahdollisten vaarojen vähentämiseksi. Lisäksi tätä on mahdollista soveltaa myös vallitseviin prosesseihin järjestelmän jatkuvan parantamisen saavuttamiseksi.
Mikä on DFMEA?
DFMEA on lyhenne sanoista Design Failure Mode Effects Analysis. Tämä menetelmä auttaa tunnistamaan tuotesuunnittelun mahdolliset puutteet kehitysvaiheessa. Useimmissa tapauksissa insinöörit käyttävät tätä menettelynä tutkiakseen mahdollisuutta suunnittelun epäonnistumiseen todellisessa tilanteessa tai käytössä.
DFMEA:n ensisijaiset työkalusuunnittelijat ovat DFMEA-matriisi. Tämä matriisi esittelee rakenteen liittyvien tietojen kokoamista ja dokumentointia varten, mukaan lukien tekniset tiedot, julkaisupäivät, tarkistuspäivämäärät ja tiimin jäsenet. Yleensä DFMEA on teknisen asiantuntemuksen tiimityötä ja luultavasti monialainen tiimi. Lisäksi DFMEA ei luota prosessiohjauksiin mahdollisten suunnitteluvirheiden voittamiseksi
Mitä yhtäläisyyksiä PFMEA:n ja DFMEA:n välillä on?
- PFMEA ja DFMEA ovat kahdenlaisia virhetilan vaikutusten analyysiä.
- DFMEA:n ja PFMEA:n perusvaiheet ovat samanlaisia, mutta niillä on kaksi eri sovellusta.
- Sekä DFMEA että PFMEA osoittavat mahdollisia virheitä, riskien vakavuutta, olemassa olevia valvontatoimia, suosituksia ja parannuksia suositeltujen toimenpiteiden jälkeen.
- Molempien perimmäisenä tavoitteena on vähentää tai välttää suuria tuote- ja tuotantohäiriöitä.
- Nämä menetelmät voivat myös alentaa suunnittelu- tai käyttökustannuksia.
- Lisäksi DFMEA ei ehkä korjaa kaikkia vikoja. Nämä viat voidaan siirtää PFMEA:lle tuotteen parantamiseksi tarvittavien toimenpiteiden suorittamiseksi.
Mitä eroa on PFMEA:lla ja DFMEA:lla?
Pääasiallinen ero PFMEA:n ja DFMEA:n välillä on, että PFMEA sisältää prosesseja, kun taas DFMEA sisältää tuotesuunnittelua. DFMEA:n ensisijainen tavoite on paljastaa mahdolliset tuotesuunnittelun epäonnistumiset, kun taas PFMEA:n ensisijainen tavoite on paljastaa prosessien mahdolliset viat. DFMEA:n peruskatsaus tehdään tuotekaavion avulla, kun taas PFMEA:n prosessin vuokaavio. Toinen ero PFMEA:n ja DFMEA:n välillä on se, että PFMEA tapahtuu toimintatasolla, kun taas DFMEA tapahtuu kehitysvaiheessa.
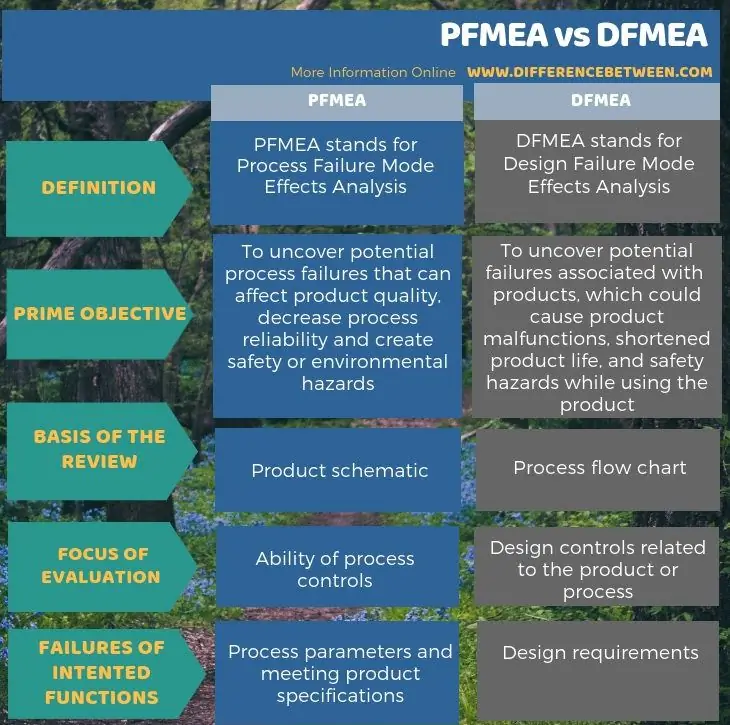
Yhteenveto - PFMEA vs DFMEA
Avainero PFMEA:n ja DFMEA:n välillä on, että PFMEA auttaa analysoimaan tietyn prosessin mahdollisia vikoja toimintatasolla, kun taas DFMEA auttaa analysoimaan tuotesuunnittelun mahdollisia virheitä suunnittelu- ja kehitystasolla. Lisäksi nämä menetelmät alentavat tuotantokustannuksia ja sekä mahdollisia epäonnistumisia tuotelanseerauksissa.